Working on offshore wind farms
Offshore Wind Farms
For more than a century the world has explored the seas and oceans to discover and subsequently produce oil and gas fields. Due to the energy transition to renewable energy sources, those same locations are once again in focus, but instead of building platforms that serve the oil and gas industry, wind turbines and wind parks are being build.
Obviously experiences gained with offshore oil & gas construction are now used to construct these wind turbines and wind parks. Thus Allnamics’ knowledge and experience with offshore foundation design, construction and testing is a valuable commodity, especially when it comes to the installation of monopiles, a special focus area of Allnamics.
For more information on the possibilities Allnamics Offshore Services can offer for your project, please contact Joost Bakker at jbakker@allnamics.com
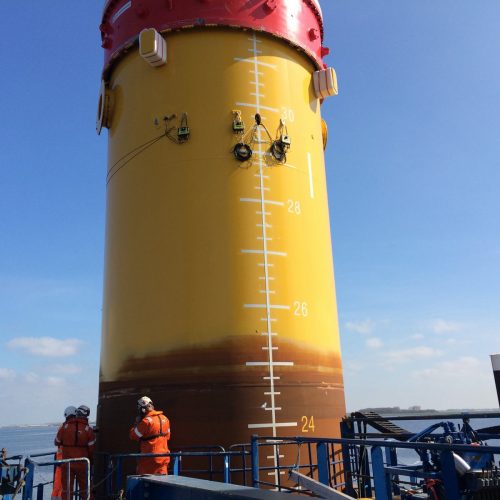
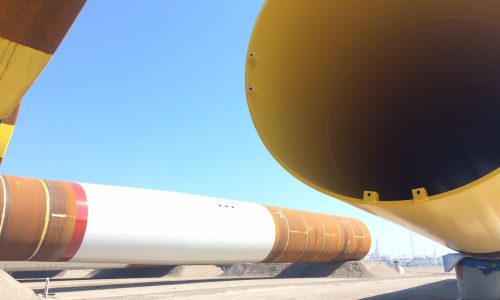
MonoPiles
Allnamics has been involved in many projects where monopiles formed the foundation of the offshore structures. Given our knowledge and experience with this type of foundations, Allnamics has become a sought-after consultant for the installation of large diameter monopiles (such as the 22-m (72-ft) diameter open pipe piles that were used for the Hong Kong-Zhuhai-Macau Bridge Project). Many of these monopiles are installed with vibratory hammers and Allnamics’ pile driving prediction software provides a unique tool to simulate this.
Want to know more? Contact Joost Bakker at jbakker@allnamics.com
Fatigue analysis, Prediction and Monitoring
During its lifetime an offshore foundation pile is continuously loaded by dynamic forces as a result of the wind, current and wave action. Fatigue is therefore an important design factor.
During pile driving the stress variations lead to fatigue as well and therefore this aspect should be analyzed. .
Allnamics can perform this fatigue analysis in two ways:
- By predicting the stress levels during installation as part of the pile driving prediction for impact hammer (PDP) or vibratory hammer (VDP) and its effect on the fatigue of the (mono)pile
- By measuring the real stress levels and their changes during pile driving, by performing PDA or VDA during installation. For measurements at certain spots additional spot monitoring can be applied as well, e.g. at locations with a diameter or wall thickness change, connection crowns, welds, or flange.
Want to know more? Contact Joost Bakker at jbakker@allnamics.com
Offshore Vibratory Driving Prediction
Nowadays, the usage of offshore vibratory hammers is no longer limited to just positioning and setting up a pile. Whereas until recently an impact hammer was used to actually drive the pile, the vibratory hammer is used more often to perform this task, even to drive the pile until the final penetration depth.
Similar to pile driving predictions for impact hammers, the pile installation by means of a vibratory hammer can be simulated. With comparable results to PDP, one can study the efficiency of a vibratory hammer, the maximum reachable penetration (or refusal) depth, the maximum stresses, and the contribution of these stresses to pile material fatigue. Using the AllWave-VDP software, the algorithms of which reflect a large database of predicted and measured results leads to reliable predictions.
Vibratory Driving Predictions will result in efficient pile design, including an efficient pile driving process with the appropriate vibratory hammer, without unexpected troubles.
For more information about our offshore vibratory driving predictions please contact Peter Middendorp at pmiddendorp@allnamics.com
Offshore Pile Driving Prediction
Pile Driving Predictions are performed to predict the pile, soil, and pile driving hammer behavior during the installation of foundation piles, including large diameter monopiles. By doing this during the engineering stage, problems and augmented costs during installation can be avoided. The pile driving hammer must be able to deliver enough energy to install the pile to its designed penetration depth. At the same time pile stresses during installation should be kept within acceptable limits. For the dynamically loaded foundations, such as monopiles of wind turbines, fatigue damage is to be considered as well and therefore the pile stresses during installation should be limited.
By making Pile Driving Predictions using the AllWave-PDP software, answers to these types of questions can be generated by modeling the pile, soil and hammer and simulating the installation process. And these predictions can be made for offshore piles in the same way as they are done for onshore applications.
For more information about our offshore pile driving predictions please contact Joost Bakker at jbakker@allnamics.com
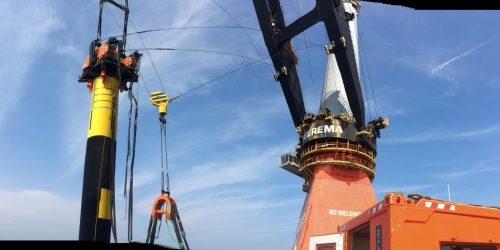
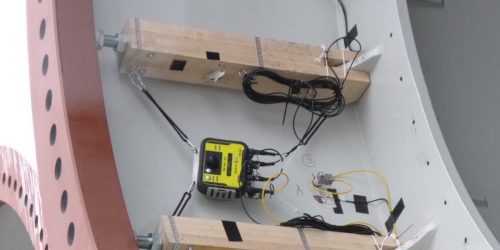
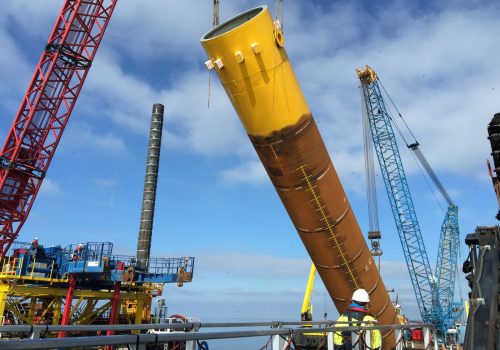
Offshore Pile Driving Analysis (PDA) or Pile Driving Monitoring (PDM)
Whenever a pile is driven it is important to know that the installation went well and this obviously also applies to offshore constructions. To ensure that this is the case measurements can be taken during pile driving (Pile Driving Analysis or Monitoring: PDA) and these measurements can then be further analyzed for additional information. This can be done whether the pile is driven with an impact hammer or a vibratory hammer.
After driving, the bearing capacity will increase with time (due to set-up). By monitoring during a redrive, the static pile/soil behavior and accordingly its static bearing capacity can be obtained by analyzing the measurements using the signal matching process with the AllWave-DLT software (a so-called High Strain Dynamic Test, commonly referred to as a Dynamic Load Test).
Want to know more? Contact Joost Bakker at jbakker@allnamics.com
Offshore Vibratory Driving Analysis (VDA) or Vibratory Driving Monitoring (VDM)
When piles are installed by means of a vibratory hammer, instead of an impact hammer, VDM and VDA can still be performed.
During Vibratory Driving Analysis all information during installation is monitored, including performance and behavior of pile, soil and vibratory hammer. Monitoring of pile stresses (and their contribution to fatigue of the pile material), pile penetration (both in absolute terms and as a function of time), and hammer frequency and efficiency are just a few of the parameters to ensure quality control for piles installed with a vibratory hammer.
Want to know more? Contact Rob van Dorp at rvandorp@allnamics.com
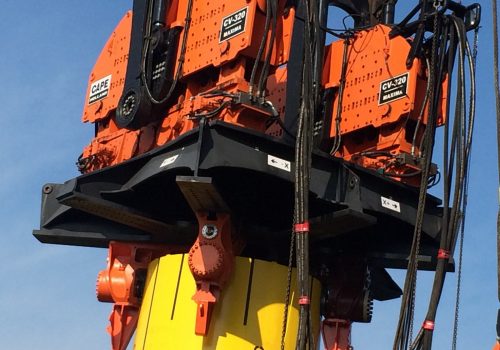
Offshore Dynamic Load Testing (DLT)
After initial developments in the 1960s, Dynamic Load Testing evolved into a mature testing method during the 1970s and 1980s. At that time offshore structures were built to explore and produce oil and gas at locations with, until then, unknown soil conditions. Since static load tests could not be performed underwater an alternative had to be developed, and Dynamic Load Testing has become a widely accepted pile testing methods
Allnamics founders are pioneers in this field and played an essential role in the development of various monitoring systems from the original FPDS (Foundation Pile Diagnostic System) to the current Allnamics’ PDR.
The main objective of performing a Dynamic Load Test is to obtain information about the pile behavior during (static) loading. Measurements during a redrive, i.e. after set-up of the soil, are then used to assess the static behavior of the foundation pile, using the signal matching process with the AllWave-DLT software.
Want to know more? Contact Joost Bakker at jbakker@allnamics.com
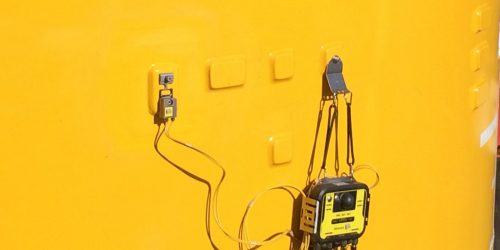
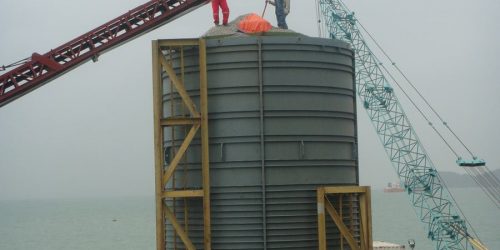
Offshore Statnamic Loading Tests
For the high capacity of offshore foundation piles and monopiles, Allnamics make use of the StatNamic pile testing method. StatNamic is a Method of Rapid Load Testing. With this pile load test method, loads up to 65 MN, and in the near future up to 150 MN, are possible.
Do you want to know more about StatNamic or StatRapid pile load testing or Rapid Load Testing in general? Contact Peter Middendorp at pmiddendorp@allnamics.com
Offshore Monitoring Equipment
The offshore monitoring methods have been developed around the in-house developed PDR (with an external Wi-Fi antenna and internal data storage). Depending on the type of sensors, the PDR can act as a full PDA system (Pile Driving Analysis, with sensors to monitor strain and accelerations, under or above water level), a VDA system for Vibratory Driving Analysis, or a system for pile load testing: static, dynamic and Rapid Load Testing.
Want to know more? Contact Joost Bakker at jbakker@allnamics.com
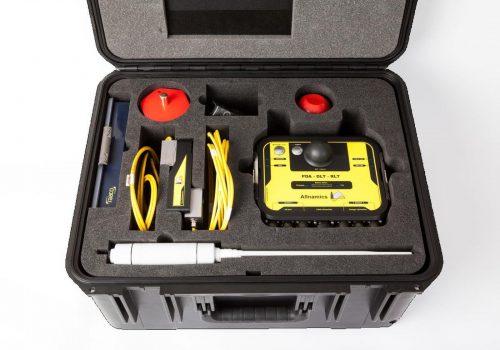
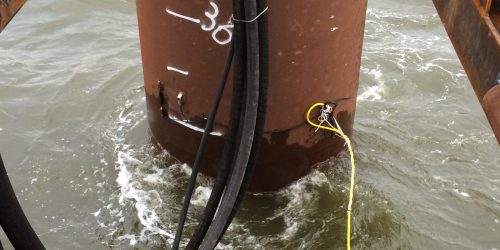
Under Water Monitoring
When under water hammers are used to install the offshore piles, the monitoring sensors need to be waterproof as well. Allnamics developed special sensors that are certified to be waterproof at depths up to 500 m.
Want to know more? Contact Joost Bakker at jbakker@allnamics.com
Offshore Pile Instrumentation
Many parameters can be monitored during and after installation of offshore foundation piles. Allnamics can provide instrumentation to address special project requirements. For more information about the possibilities that Allnamics Offshore Services can offer for your project?
Contact Joost Bakker at jbakker@allnamics.com
Read more about Allnamics Offshore Services
More projects, papers and research results are described on this website of Allnamics. If you want to read more, check out the links below, or see more projects in news or under projects:
- Windpark (OWF) Fryslan
- Riffgat Wind Farm, Germany
- Wikinger, Baltic Sea
- DOT Project
- Offshore PDA and DLT for a tidal station in the UK
Or contact Joost Bakker at jbakker@allnamics.com
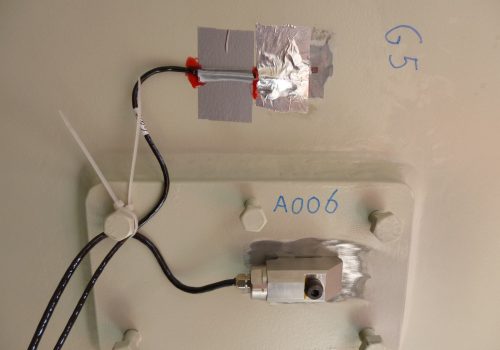
PAPERS EN ARTICLES
Allnamics has made many contributions to international conferences. These publications are available via the Allnamics database. A selection from that:
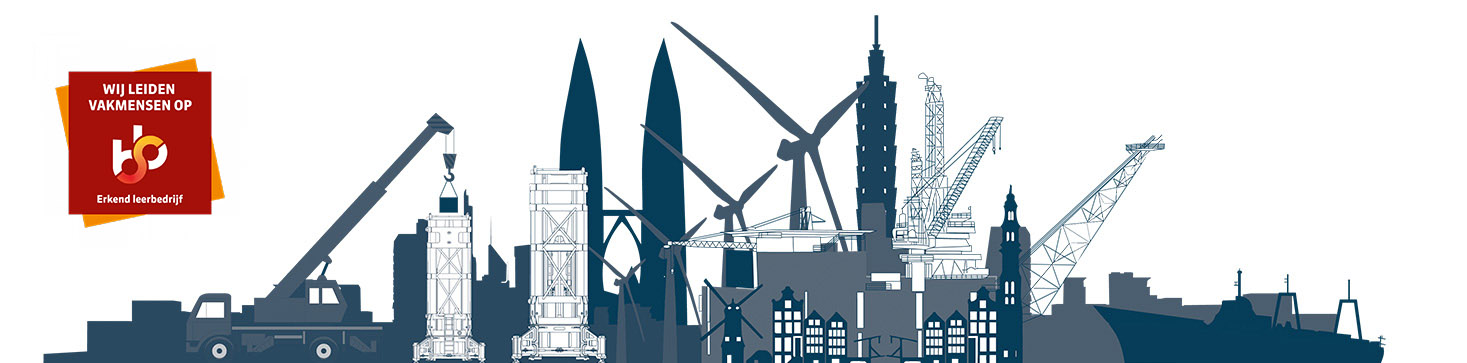