In March 2017 Allnamics performed SLT-monitoring for a client in Amsterdam. The timber piles under an existing building were presumed to have inadequate static bearing capacity and therefore needed to be tested.
Most buildings in the center of Amsterdam have wooden piles foundations with approx. 12 m long timber piles that are driven into so- called first sand layer. However, at some locations this first sand layer is not there and in that case piles of that length will have inadequate (toe) bearing capacity.
To testing an existing wooden pile foundation specialized monitoring equipment is required. The process begins by creating a small excavation pit to expose the top of the timber pile and given the high water table continuous dewatering is necessary to keep the pile top exposed.
The pile head is then cut off and prepared so a steel plate can be placed to ensure that the pressure applied by the hydraulic jack is equally distributed over the pile head. On top of that steel plate a load cell and a hydraulic jack are placed, while below the plate a special reference frame is constructed to mount the potentiometers that will monitor the displacement.
The load cell and the potentiometers sensors are connected to a PDR (either a Quad-PDR or a standard PDR) that is connected to a laptop with the Allnamics-SLT software. The software is able to show all test data both in tabular and graphical format.
During the test, the pile load is controlled manually in accordance with the client specification and local regulations. The typical test results are shown in the graphs below.
The ultimate load capacity can be then determined as specified by the client. This is commonly defined as the load that causes a displacement of 10% of the pile diameter, but it can also be defined in accordance with various other methods, such as Chin-Kondner, Davisson, Van Delft, or Van der Veen.
Allnamics developed for this type of Static Load Test a monitoring equipment set with a load cell that has a very high accuracy (+0.23kN) over the relatively small operating range (up to 1 MN), which is more than adequate considering the actual loads on these timber piles.
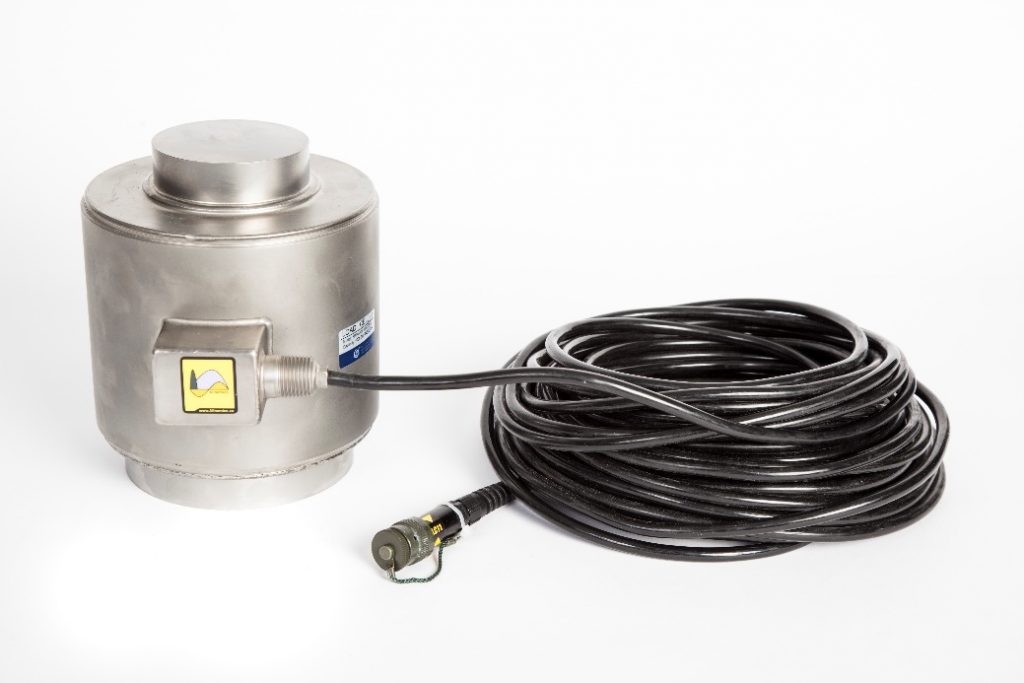
Photo 1 : The load cell with cable and USID connector for connection on the PDR
Inside the load cell’s connector is a memory chip that contains information on the load cell such as calibration data and various information for checking the proper functioning of the load cell.
The load on the pile can also be checked using a pressure sensor attached to the hydraulic system. For this purpose Allnamics selected a sensor capable of monitoring hydraulic pressures up to70 MPa with an accuracy of 28 kPa.
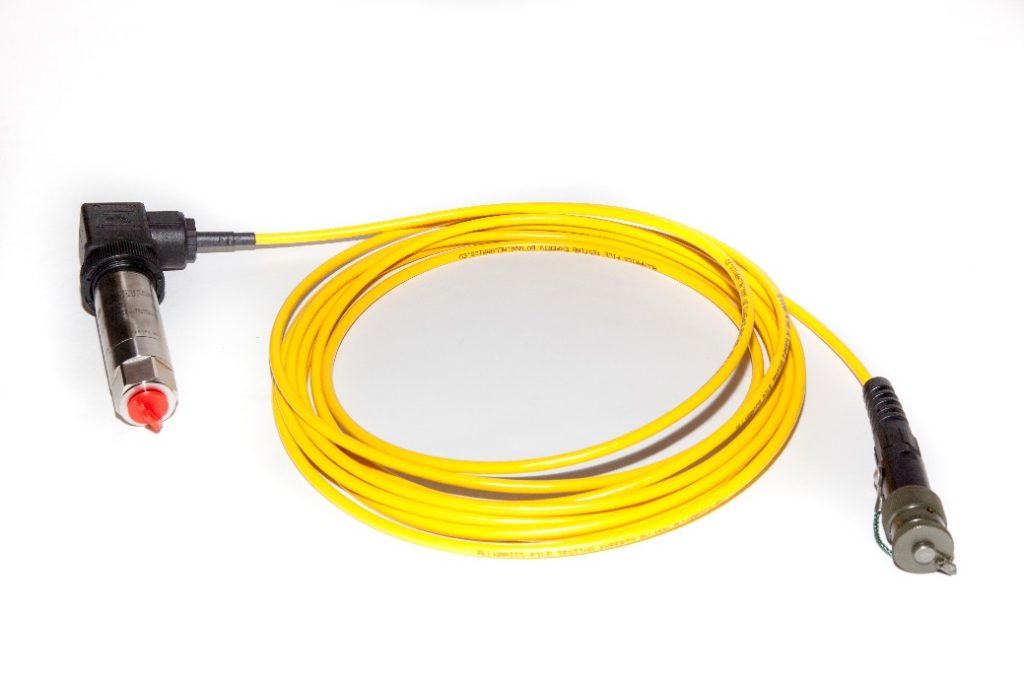
Photo 2 : The pressure sensor with cable and USID connector for connection to a PDR
Apart from monitoring the force on the pile head accurate monitoring of the pile head movement is essential. For this purpose Allnamics selected potentiometers with a range of 200 mm and an accuracy of 0.1 mm.
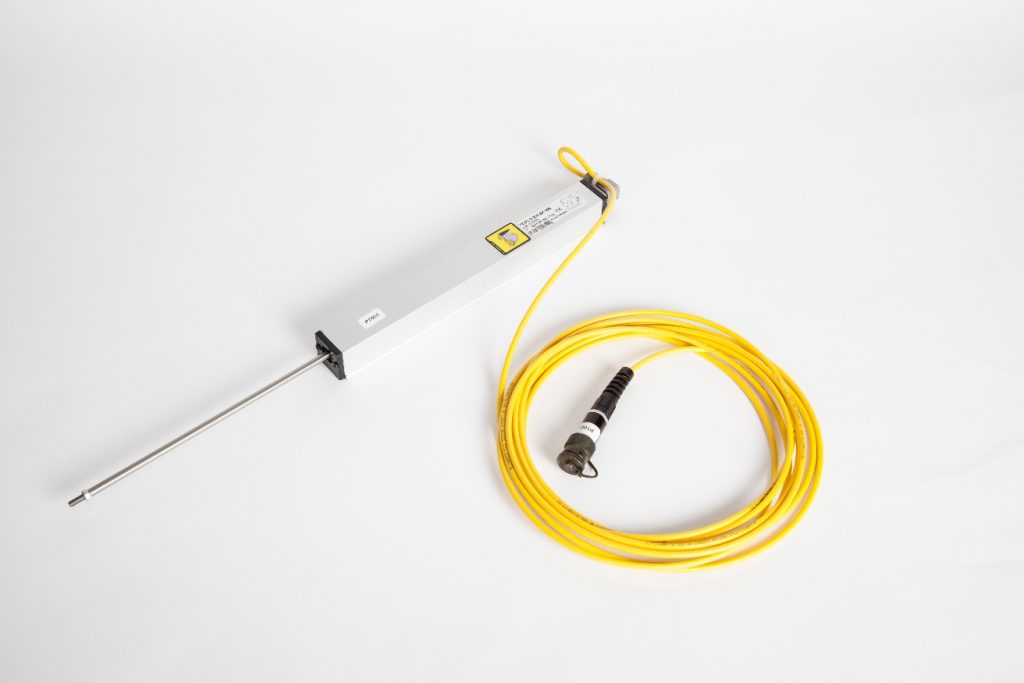
Photo 3 : The potentiometer for monitoring the displacements during the pile test
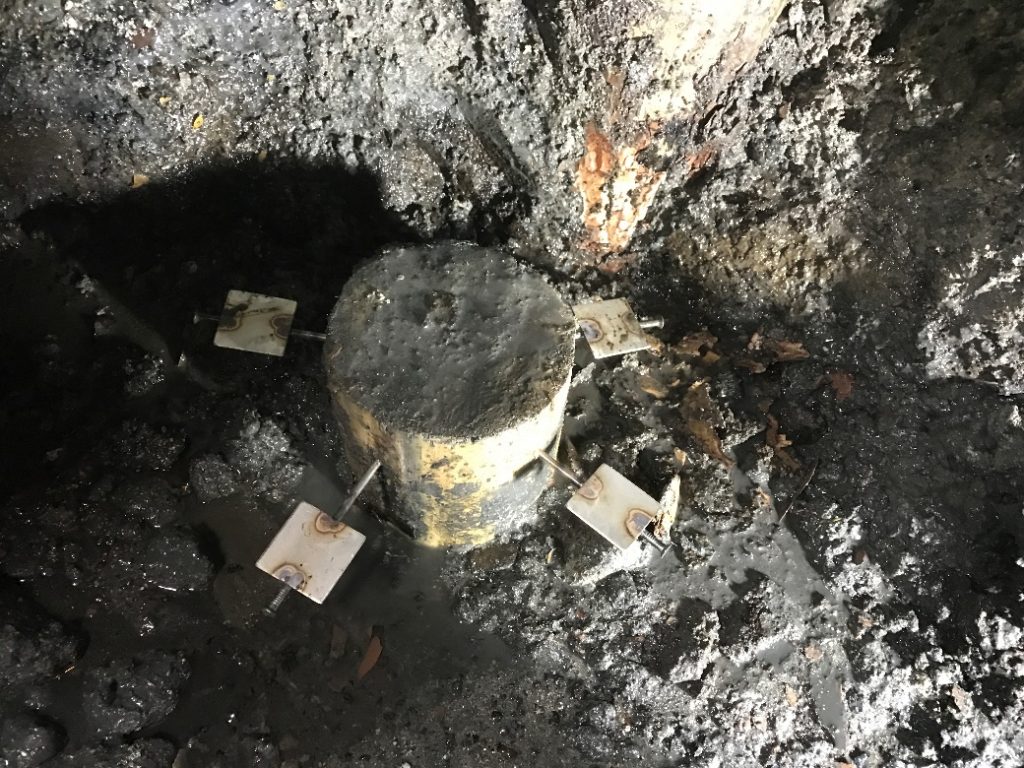
Photo 4 : The wooden pile cut off and 4 plates for the potential meters are placed around the pile head.
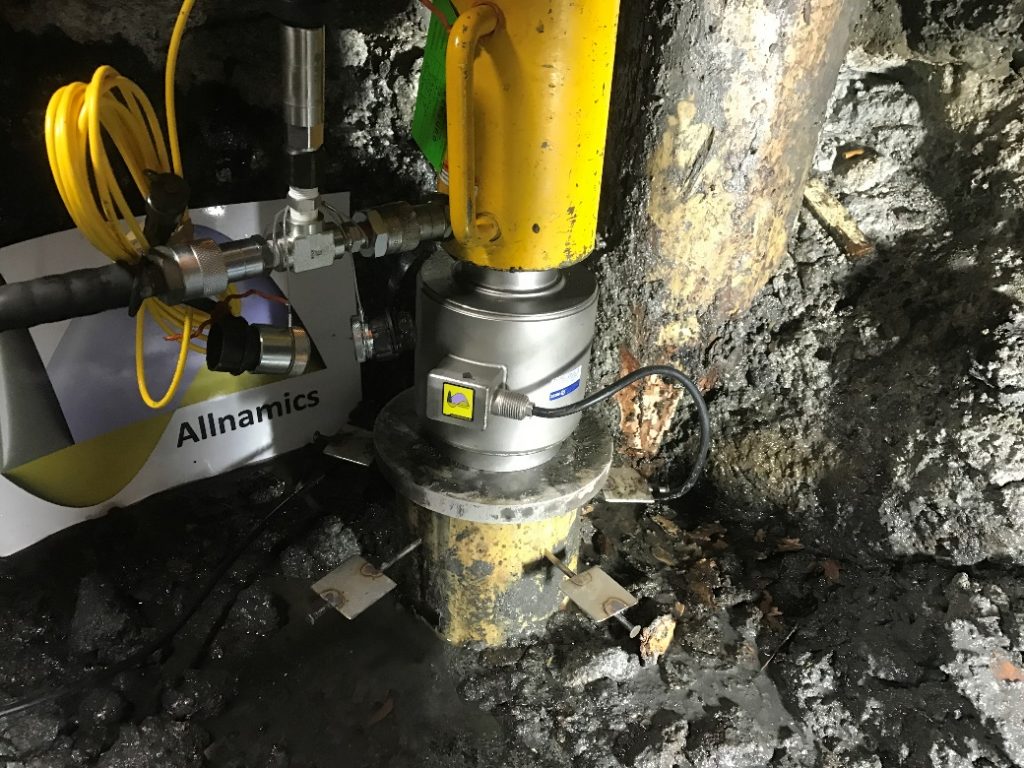
Photo 5 : The pile with steel plate, load cell and yellow piston with the pressure sensor on the hydraulic system.
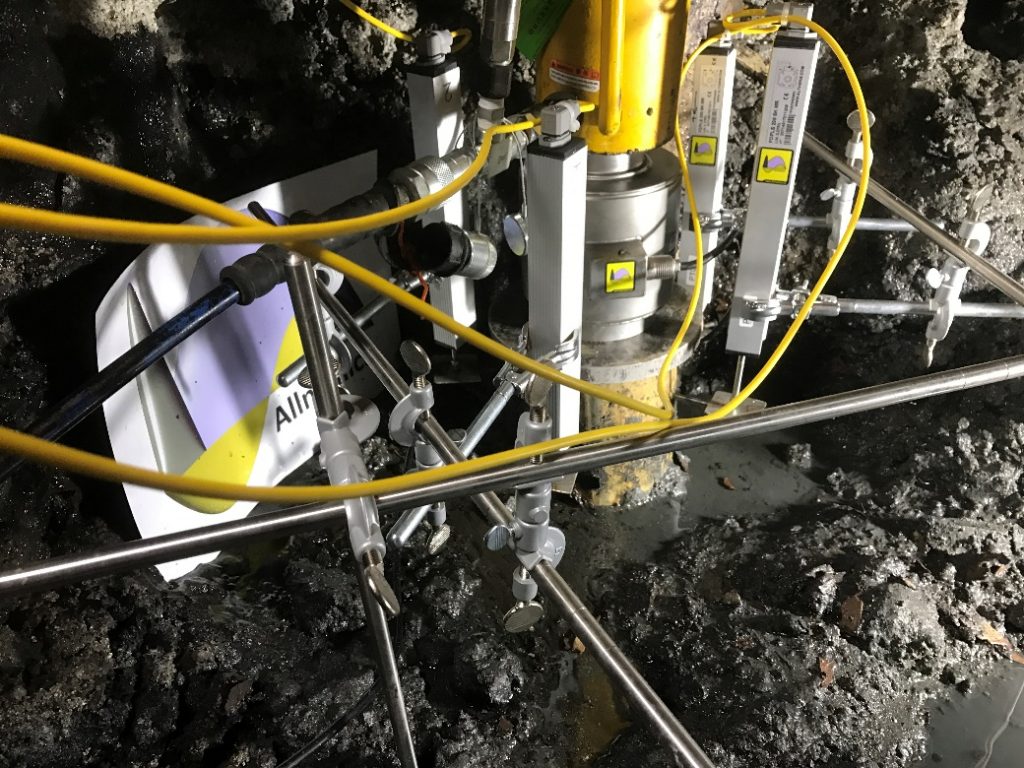
Photo 6 : The pile with a reference frame and potential meters installed
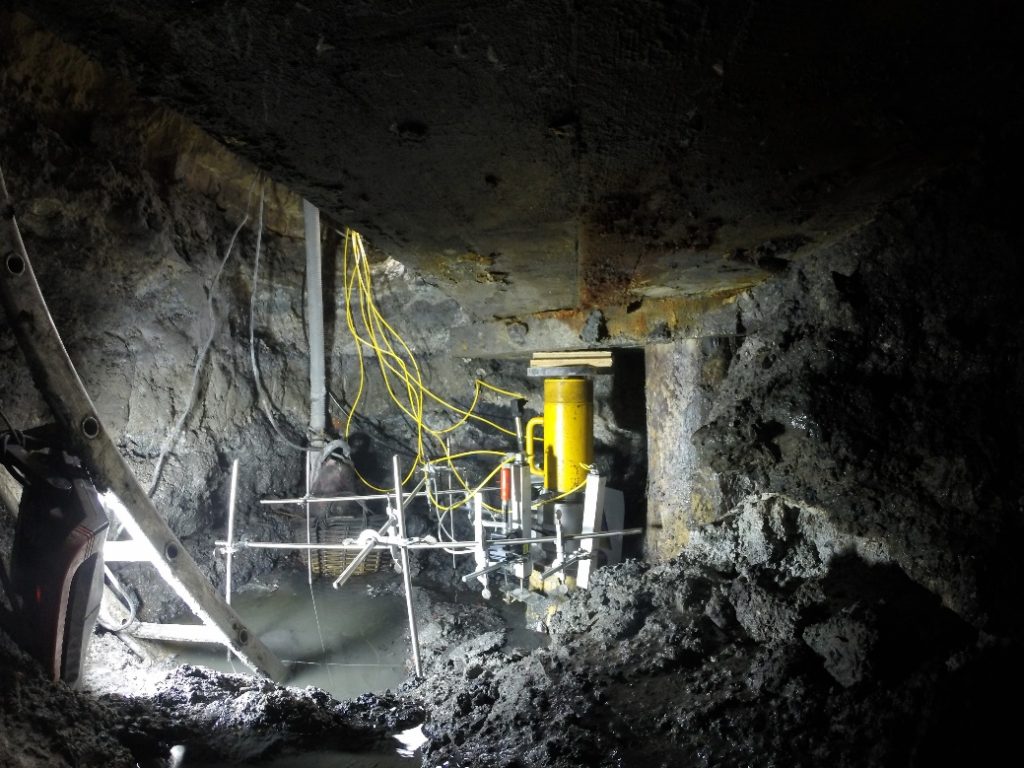
Photo 7 : Overview of the Static Load Test underneath an existing building.
Video 1 : How to make a setup for a Static Load Test. Watch this video.
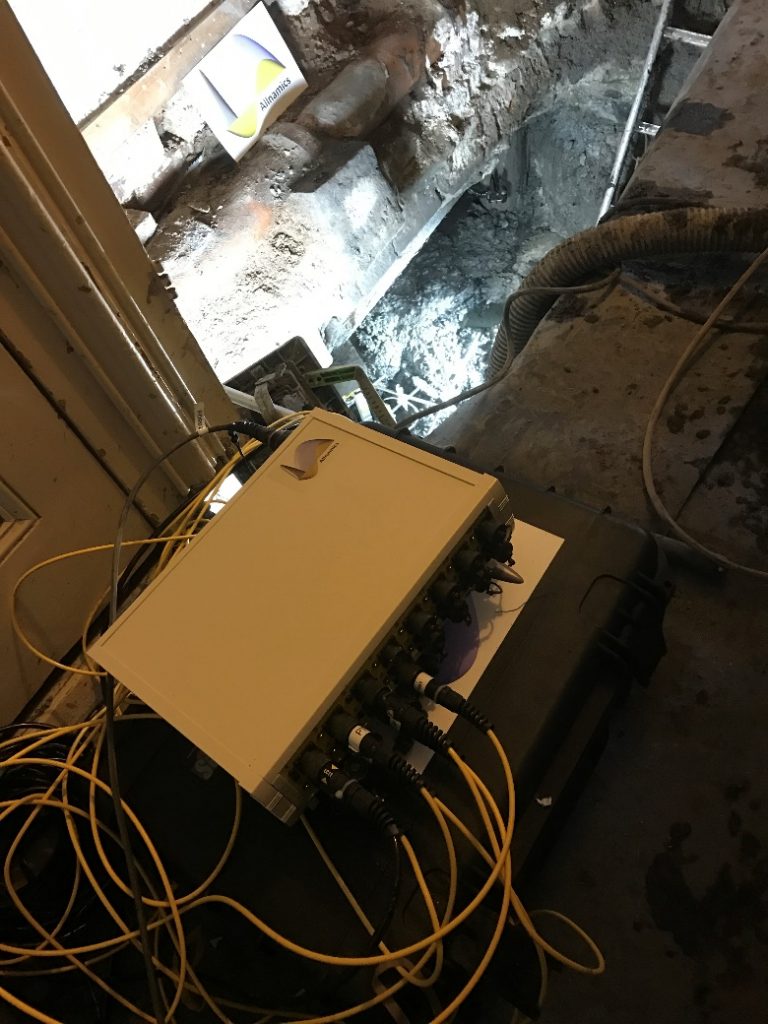
Photo 8 : The Quad-PDR with at the background the test location underneath the existing building.
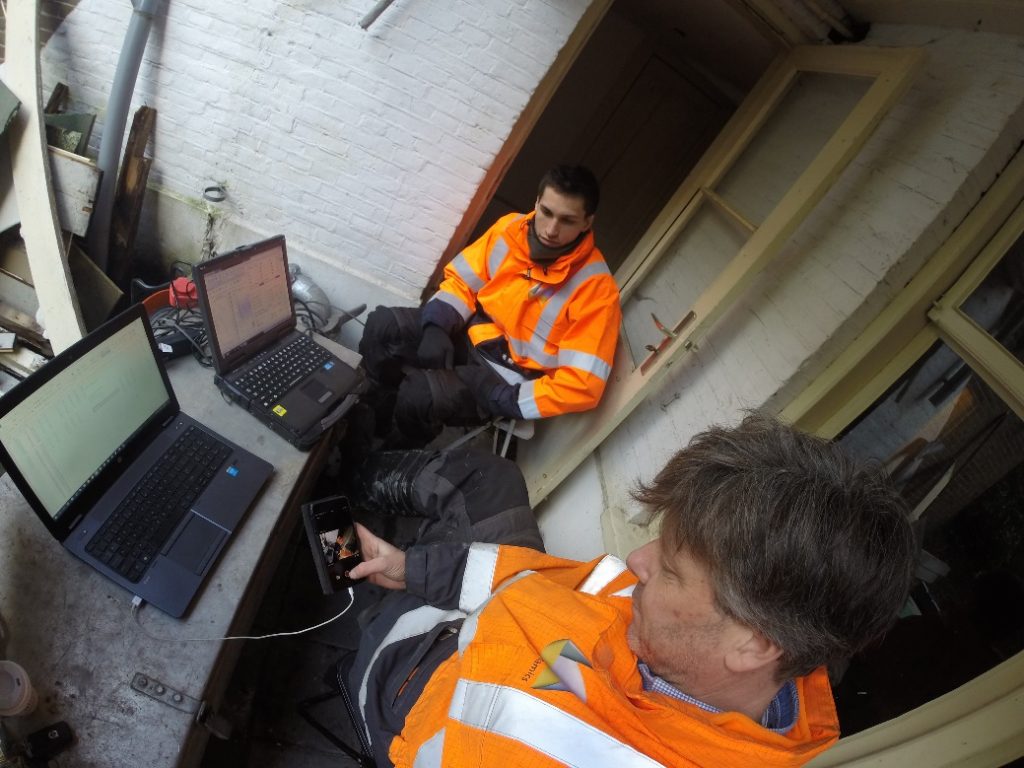
Photo 9 : The measuring specialists behind the monitoring software.
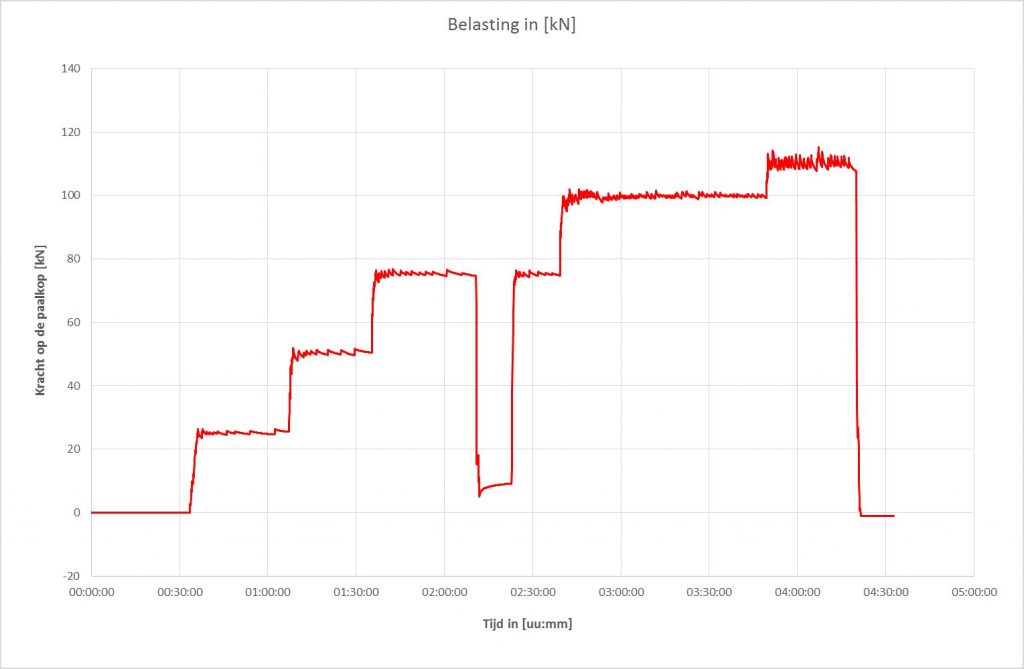
Graph 1 : The measured force of the load cell in time
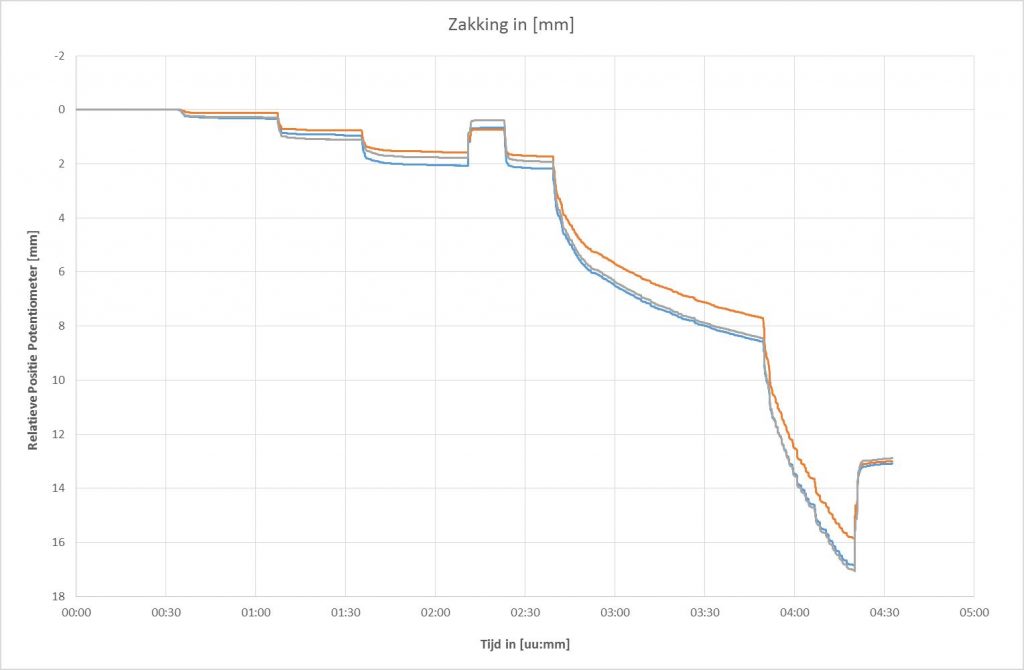
Graph 2 : The measured positions of the potential measurements in time
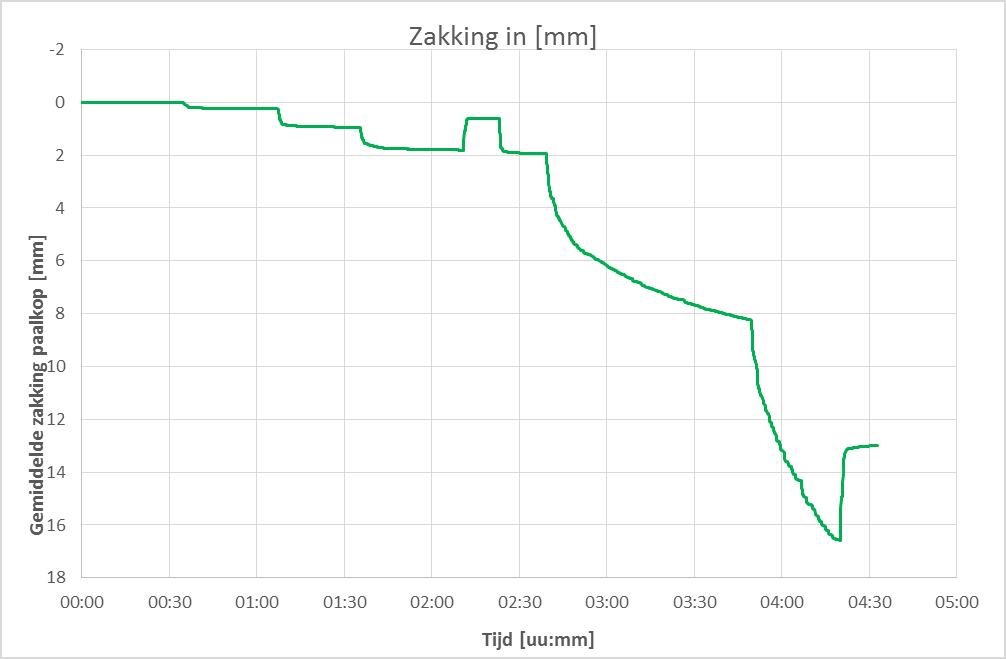
Graph 3 : The calculated average settlement of the pile head in time
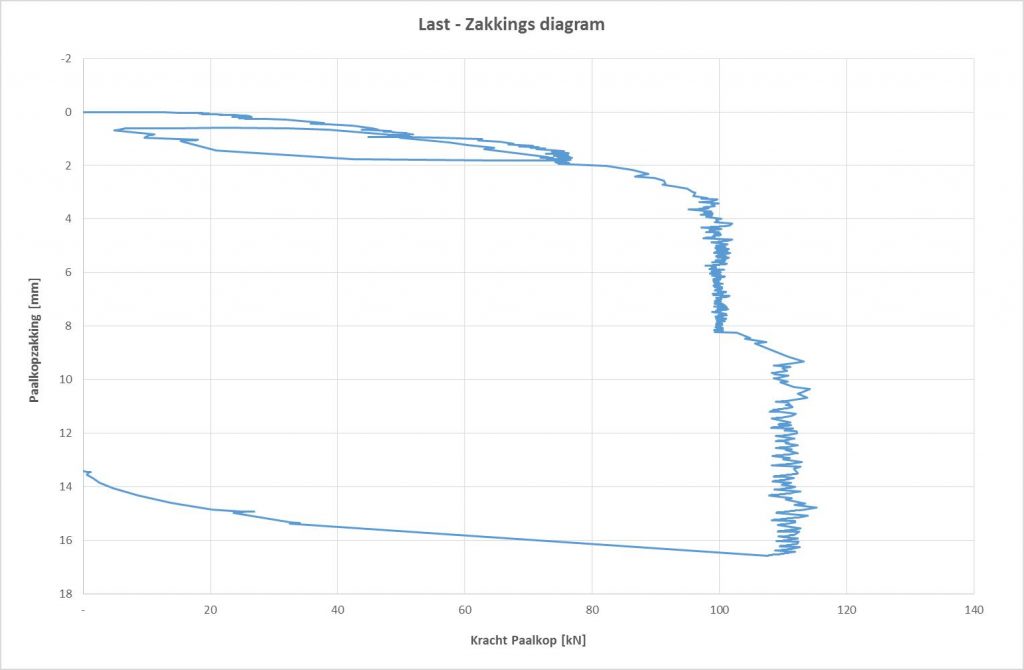
Graph 4 : The load – settlement diagram of the wooden pile
If you are interested in Static Load Testing please contact us.