PILE DRIVING SIMULATION FOR VIBRO HAMMERS
While pile driving simulations for piles driven with an impact hammer are standard practice, the same cannot be said for piles that are vibrated into the ground. And so more often than not we rely on experience to select a (over dimensioned / oversized) vibratory hammer for a particular application and then hope that we can drive the pile to the required depth. With Allnamic’s AllWave-VDP software you can actually be sure that this will be the case. The installation process is simulated and the predictions are as you would expect for any other pile driving simulation with impact hammers.
Big, bigger, biggest: all offshore equipment increases over time:. an upending tool combined with a 920 kgm vibratory hammer. All to be used in simulation of the installation process of AllWave VDP
Driving of a 22 m diameter monopile worked out to be successful after
go-ahead by AllWave Pile Driving Simulation software from Allnamics (2011).
Over the years many projects has been both predicted and measured, resulting to improved soil models and improved methods for determination of the soil parameters from soil investigations. By frequently closing the learning loop (prediction, measuring, post-analysis), the predictions for the pile-hammer-soil behavior is nowadays reliable and accurate.
ALLWAVE-VDP
AllWave-VDP is a software program specifically for onshore and offshore driveability studies for pile driving with vibratory hammers.
FEATURES
- Wave equation software based on the Method of Characteristics
- Product of more than 40 years continuous in-house development
- Highly accurate vibratory hammer modeling
- Extended library for vibratory hammers and steel (sheet)pile profiles
- Various soil modeling options, incl. TNO and Smith
- User friendly software interface to produce predictions
- Standardized output options
- Advanced options for research purposes
VDA: PILE VIBRATORY DRIVING ANALYSIS
To monitor the pile installation process with a vibratory hammer, Allnamics has developed Vibratory Driving Analysis (VDA) equipment, the equivalent of Pile Driving Analysis equipment for impact driving. The equipment monitors installation records (penetration speed), hammer performance (power-output, amplitude and frequency), pile data (pile stresses) and soil resistance during driving.
Allnamics VDA allows not only control of the vibrodriving process, but the recorded data can also be used for subsequent Fatigue Analysis and Vibratory Amplitude Matching.
KEY FEATURES
- All necessary equipment (incl. a toolbox) is delivered in a single rugged case;
- Both regular and underwater sensors (suitable to depth depths of 200 m)
- Data acquisition system (the PDR):
- 4 multipurpose sensor channels
- 6 hours of operational battery
- 200 m Wi-Fi range
- Internal solid state memory backup
- Suitable for other testing and monitoring applications
- Allnamics-VDA monitoring software
- Automatic reporting tool
WORKING PRINCIPLES
A set of combined acceleration &strain sensors and the PDR data acquisition system are bolted to the pile to allow for:
- Live monitoring of the pile vibrodriving process
- Real time sensor status control
- Possibility to export the results for post-processing for Fatigue Analysis and Vibratory Amplitude Matching
TEST SETUP
Prior to the start of the monitoring holes are drilled, and the sensors and the PDR are mounted (note: the drilling machine is not included in the single rugged case). During monitoring the data can be transmitted to the field computer in various ways as shown in the figure below, or recorded in the PDR for downloading once the pile driving has been completed.
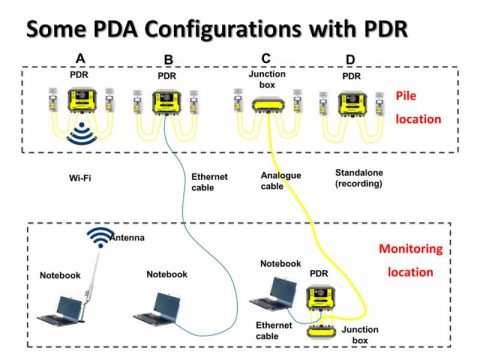
ALLNAMICS COMBINED SENSORS
Allnamics uses combined sensors to monitor accelerations and strains in a pile during installation. This simplifies the mounting process as only two bolts are required for each set of accelerometers and strain gauges. At the same time the sensors can be easily separated, allowing replacement of the sensor.
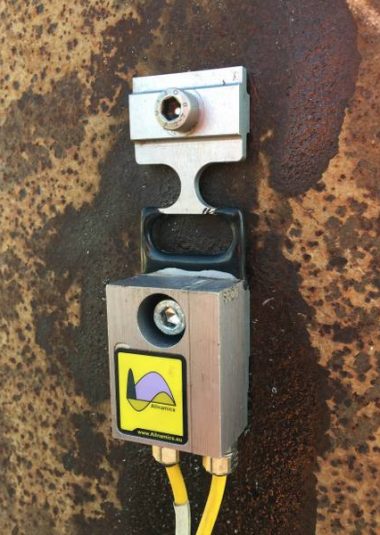
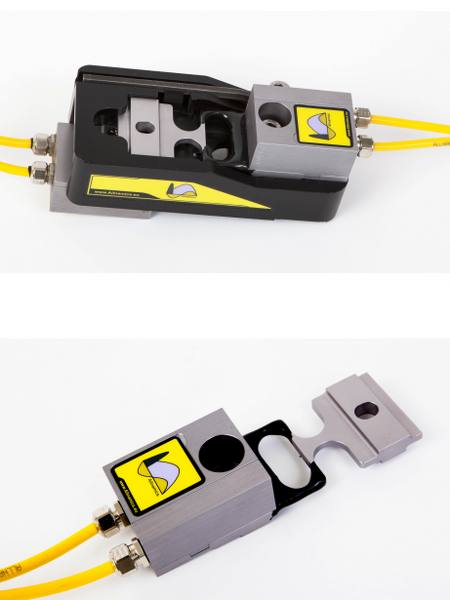
FEATURES
- Spacing tolerance to adjust to site conditions
- Protective housing for transport and mounting
- Sensors are equipped with USID, automatic ID/Calibration
- Range strain sensor ± 1500 micro strain
- Range piezoresistive accelerometer ± 500g
- Dedicated sets for above water or underwater applications; underwater sensors are suitable for water depths up to 200 m.
Projects
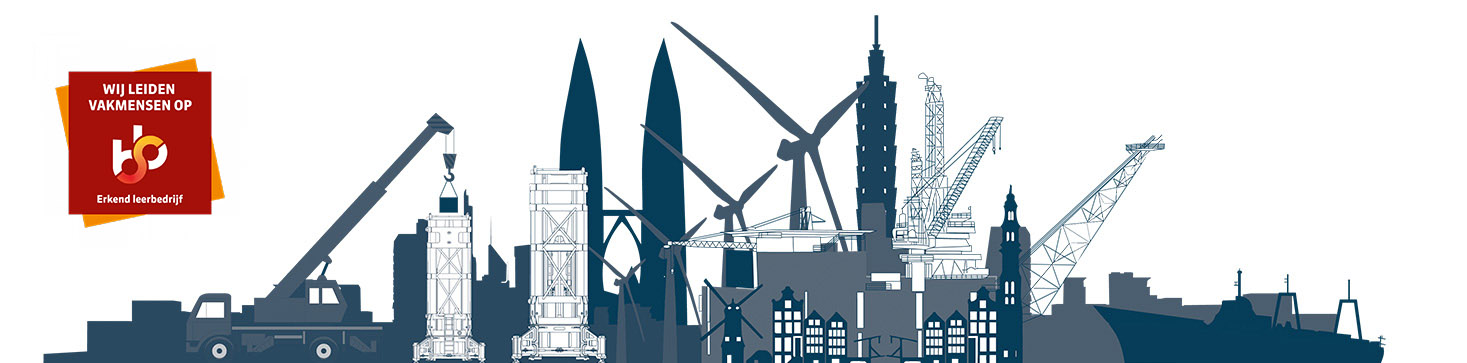